Introduction - FAA Repair Station No. S2DR551J - 40 employees
- EASA Approved - 145.4883
- 9 years average experience - Licensed A&P mechanics
- EASA MIST Audited-Operator Audited
- Approved Repair Station Number 647315 for Boeing Commercial Airplane Group
- OEM Support Provided on Mechanically Operated Flight Deck Windows & Galley Inserts
- OEM Support Provided for Galley Inserts, Modifications Programs, Warranty and Routine Repair
- FAA Part 145 Operations Specifications listed windows: Airbus, Boeing, Douglas, Fokker, Lockheed
- Full line support for coffee makers, ovens,various accessories and Water/Waste Systems
- Authorized Goodrich Lighting Modification Center
Since 1993,
Soundair Repair Group has been specializing in the repair, overhaul and inventory management of commerical jet transport flight deck windows and galley inserts. Soundair recently relocated to a modern state-of-the-art 18,000 square foot facility designed and built specifically for performing maintenance on aircraft parts and components. Each production area has been specifically designed for their product types. Those areas include the window, coffee maker, oven, lavatory component, and accessory product lines. Segregated and controlled areas include bulk storage, bench stock, parts, NDI, technical documents, and archives.
New Building
Major building features and equipment include gas fired heat and air conditioning, high output fluorescent lighting, sealed concrete shop floors, insulated ceilings and doors, smoke and fire protection per code, and a fully monitored security system. The paint room features two walk in spray booths coupled to a 10,000 CFM modulated output direct gas fired air make-up unit, with atmospheric control provided by a PhotoHelic pressure monitor. Other features include an IT-200 automatic paint gun cleaner, 120 CFM thermal mass air dryer, coalescing filter and a building-wide distribution manifold. Parts and components are cleaned for inspection using dual Maxi-Blast MBA3630PAR Recycling pressure blast cleaning systems. The office area that comprises approximately 7,500 square feet, houses all support personnel and functions for the repair station.
We have established close working relationships with the original equipment manufacturers (OEM) who have visited our facility to look closely at the product we produce. This has resulted in our being solicited by the OEM to provide frame overhaul and assembly using OEM rebuilt panels. Likewise, Soundair visits to the OEM facilities have provided us with ongoing insight of the rebuild process, rebuild candidate evaluation, and new process developments underway.
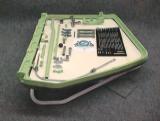
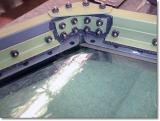
Our operator customers will attest to the superior service and attention to their needs, while our OEM customers will attest to the unsurpassed product quality.
Of particular importance is our Galley Products Department is staffed by factory training technicians, which further assures that our product is capable of achieving maximum reliability. Supporting that, Soundair has developed numerous modification programs and troubleshooting procedures that have successfully resolved product performance issues. Our operators do realize the benefits of this approach through improved MTBR, MTBF, and reduced per hour operating costs.
FAA AMT Awards Program
In an effort to maintain the highest levels of aviation safety, The FAA Flight Standards Continuous Airworthiness Maintenance Division (AFS-300) developed the AMT Awards Program to encourage AMT employees and employers to participate aggressively in available initial and recurrent training and courses.
The FAA recognizes those employees and employers by issuing awards to those who successfully complete and foster initial and recurrent training. Awards are issued on a yearly basis for training received that calendar year.
Soundair Repair Group has been awarded the highest level of achievement for the AMT Awards Program, receiving the Diamond Award for employee participation for six years running.
The FAA has also given special recognition to Soundair. Special Achievement Awards have been presented in recognition of 6 straight years of 100% employee participation in the AMT Awards Program. This high level of aviation safety and regulatory awareness is an integral part of the Soundair philosophy, and is unique to only a very few companies. We also have on staff a certified FAA Aviation Airworthiness Safety Counselor. We are proud to be an active participant and industry leader in this important program and approach to aircraft component maintenance.
Repair and Overhaul
Soundair is proud to offer the following Repair and Overhaul Services:
- Sliding Windows
- OEM Rebuild
- Galley Products
- Accessories Support
P R I D E
Products Reflect Individual Daily Effort
Sliding Window Overhaul
Soundair has been overhauling commercial transport flight deck windows for over 10 years. During this time, much development work has occurred as needed to address the sliding and openable window assemblies.
Soundair's attention to detail addresses numerous areas where the applicable manufacturer overhaul manuals are vague or simply do not cover some detail aspects of a given sliding window's requirements to assure long-term performance and reliability.
Reliability and long term value are the basis of Soundair's approach to sliding window overhaul. We go the extra step from complete tear down, detail inspection, NDT, pre-assembly alodine and primer, through final inspection. We replace all hardware, seals, and bearings which assures smooth trouble free operation.
We offer a full 3 year warranty against all defects in material, workmanship, and functionality. This is the Soundair definition of
VALUE.
Sliding Window Samples
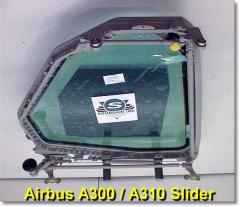
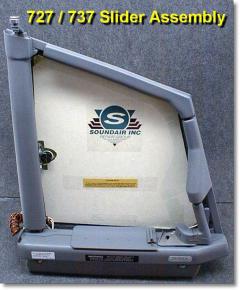
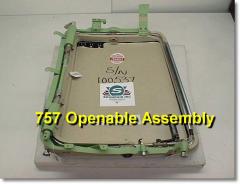
OEM Rebuild
Soundair has established close alliances with the window manufacturers who, in recent years, have developed numerous rebuild schemes for glass, acrylic, and glass/acrylic windows.
There are three types of repairs currently available for window panels:
Minor Repair: This includes the resurfacing and replacing minor components such as pressure seals, hump seals, and electrical connectors. These are commonly accomplished at the Repair Station level, and are within the scope of work performed by Soundair.
Relamination: This involves removing a minimum number of edge components relaminating the existing structural and interlayer plies, and replacing edge components. This process is not acceptable in terms of service life, as it does not address the contamination that may have originally caused the delamination to occur. Soundair does not employ this process in our overhaul programs.
Rebuilds or Major Repairs: This entails completely tearing down the window panel and reassembling it. Edge attach components are removed, the laminate disassembled, damaged plies and interlayers removed, and the salvaged components used with new components to rebuild the part using the original equipment manufacturing processes.
The rebuild process can only be accomplished in the manufacturing environment using the original detail design specifications for new windows. Each window meets the latest design configuration requirements thus assuring a service life equal to that of a factory new window. These unique processes have been reviewed and FAA approved.
Because Soundair utilizes the rebuild schemes of all our OEM suppliers, we have visibility to the strengths of each manufacturer. Utilizing this performance data, we are able to identify the best performing rebuild by manufacturer. As conditions and products change, Soundair is quick to revise our integration of rebuilt windows using only the latest developments to assure continuous improvements in the long term performance of our assemblies.
OEM rebuilt windows offer a measurable savings from that of purchasing factory new assemblies. Given the fact that rebuilt windows have a service life equal to factory new windows, the up front savings can be factored directly to lower operating costs. And because the rebuild process often takes over 60 days, Soundair carries an exchange inventory of rebuilt windows to support more immediate customer requirements.
Galley Products
Soundair also offers repair and overhaul support for galley inserts. These capabilities come with a long list of items supported by an experienced OEM trained staff. The production areas consist of three multiple bank test benches for coffee makers, one multi bank test bench for ovens, and two specially built accessory benches. All of these stations are powered by a Piller 75kVA 400Hz power supply. This gives us capability to test multiple units at one time including the ability to test the highest current ovens in operation today.
Our programs support fixed price repair and overhaul with 7 to 21 day turn times. We also maintain a pool of the most popular models for immediate exchange as needed to support critical requirements.
As with our window product line, quality and reliability are of paramount importance. Each coffeemaker receives a complete inspection, tank flush, filter change, and solenoid disassembly to assure proper operations. Additional attention is also given to general shop service which includes a complete disassembly to assure proper operation. The tank is pressure tested and inspected for leaking or bulging. It is then flushed to remove any calcium or rust build up. All internal tank parts are inspected and repaired or replaced as necessary The solenoids are disassembled and inspected and will be overhauled if required to assure proper operation while the vent valve and level sensor probes are closely inspected and serviced. The failure of these items are the leading cause of rejection from your aircraft.
We also support many of the new generation ovens from B/E Aerospace (Includes Inventum & Nordskog) to Britax (Includes Sell & Rumbold). Ovens really see the rough treatment in service, and it is not uncommon that we must replace door structure, latches, and OCM (Oven Control Module) housings. Our technicians are experienced at all levels of teardown and rebuild, including case replacement.
Galley Insert Samples
Accessories Support
Soundair Repair Group has established support on many accessories common to our customer fleets. These support items include landing light assemblies, anti-collision lights (including strobes in accordance with FAA approved flash tube replacement intervals), florescent overhead lighting, battery chargers, air stair controls, and megaphones.
We maintain exchange inventory to support emergency requirements and can often meet the needs of our operators on a moments notice.
Accessory Samples
Typical Pre-Overhaul Exchange Inventory
The following flight deck windows and galley inserts are often in stock at Soundair for immediate exchange to our operator/customers:
Complete Flight Deck Window Ship Sets:
Sliding / Openable Window Assemblies: - DC9 / MD80
- 727
- 737
- 767
- DC10/ MD11
- A300 / A310
Sliding / Openable Window Panels: - DC10 / MD11
- DC9 / MD80
- 767
- 757
Fixed Windows- 727 / 737 #3 Airgap
- DC9 / MD80 Upper Eyebrow
- DC10 / MD11 #3 Aft
- 767 # 3 Aft
- 757 #3 Aft
Galley Insert Products - 50405-100 coffee maker B/E Aerospace
- 50405-108 coffee maker B/E Aerospace
- 50505-200 coffee maker B/E Aerospace
- 416-0001-1 coffee maker B/E Aerospace
- 416-0001-9 coffee maker B/E Aerospace
- 416-0001-29 coffee maker B/E Aerospace
- 411-0001-137 coffee maker B/E Aerospace
- 411-0001-137 coffee maker B/E Aerospace
- 72011403B coffee maker B/E Aerospace
- 72011414 coffee maker B/E Aerospace
- 70212400 coffee maker B/E Aerospace
- 72067000 oven B/E Aerospace
- 72067002 oven B/E Aerospace
- 8001-06-0000 oven Britax
- 8021-06-0000 oven Britax
SOUND AIR REPAIR GROUP, LLC |
1826 Bickford Ave, Snohomish, WA 98290
United States
FAA Repair Station No. S2DR551J | |
Contact:
Greg Harwood
DIRECTOR SALES/OPERATIONS
gregh@soundair.com
Dan King
REGIONAL SALES MANAGER
dking@soundair.com